We have documented 96 different Servo Manufacturer repair reports in our Database
Servo Motor Repair
Repair Servo Motors Now
- ABB
- AEG
- Allen Bradley
- Baldor
- Bosch-Rexroth
- Elmo
- Exlar
- Fanuc
- Gettys
- Harmonic
- Indramat
- Kessler
- Pacific Scientific
- Reliance
- Siemens
In today’s fast-paced industrial landscape, servo motors play a vital role in countless applications, ranging from manufacturing and automation to robotics and precision control systems. These advanced machines require regular maintenance and occasional repairs to ensure optimal performance and reliability. At Lincoln Service, our mission is to provide excellent servo motor repair services that meet the specific needs of our clients, allowing them to minimize downtime, reduce costs, and maximize productivity.
Our Expertise and Commitment
Lincoln Service is a renowned name in the servo motor repair industry, known for its exceptional quality of service and customer satisfaction. With decades of experience, our team of highly skilled technicians possesses extensive knowledge and expertise in repairing a wide range of servo motors, including AC servo motors, DC servo motors, and brushless servo motors.
The Importance of Quality Servo Motor Repair
Servo motors are complex precision devices that require specialized care and expertise when it comes to repairs. The improper handling of motor repairs can lead to further damage, reduced efficiency, and costly downtimes. That is why it is crucial to partner with a reputable and reliable servo motor repair service provider like Lincoln Service.
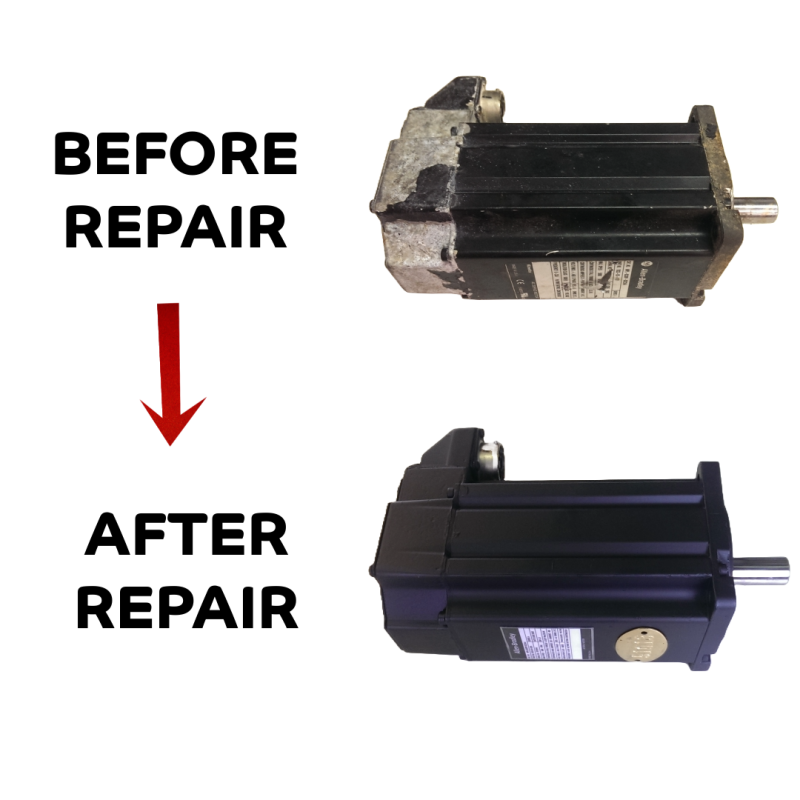
Servo Lab Repair Procedures
Servo Motor Repair capabilities
1. Data
Motor nameplate data is recorded
2. INSPECTION
A visual inspection of any damage to the motor
We check for:
- Damaged Leads/Terminals
- Worn output shaft/keyways
- Cracks in end bells or covers
3. JOB TICKET
We complete to full write up off all motor data
Including:
- All winding tests (Resistance, Meg Ω, Continuity)
- All bearing sizes
- All seal sizes
- Brake torque tests (Record Torque, winding resistance)
- Feedback Tests (Tachometer/Encoder)
4. MOTOR DISASSEMBLY
- Bearing and seal sizes are recorded
- Bearing fits are measured on shaft and End bell
- Brake torque is measured as well as resistance and Meg Ω
- More winding tests are performed (Surge and HiPOT tests)
- Stator is then washed and baked in oven (or burned out if required)
- Magnets are inspected for cracks or if loose on shaft
- Encoder is tested with either (Heidenhain PWM20, Sick PGT-11, or Mitchell Electronics equipment)
5. ASSEMBLY
- New bearings are installed
- New seals are installed
- If required, new windings are impregnated
- Brakes are rebuilt or replaced depending on manufacturer design.
- Rebuilt or New encoders are installed and aligned using:
- (Heidenhain PWM20, Sick PGT-11, or Mitchell Electronics equipment)
6. ROTOR BALANCING AND TESTING
- Rotor is run through a full vibration diagnostic
7. RUN TESTING
- Every Motor is Run for a minimum of 1 hour using one of our drives.
- We use Siemens S110, S120, IndraDrive, AB Kinetix 300, Yaskawa 7, and AMC drives
8. SERVICE REPORT
- A Final 3-page Service Report is filled out
- Pinout diagram for power and feedback is provided
- Brake torque is recorded a final time for our Service Reports
- A photo of nameplate and motor is attached
- A motor tag is installed on motor with QR code linking Service Report and Job Histories
- If requested, a YouTube link is attached to the service report of motor
- Please look at our service report to see a sample of our servo motor repair capabilities.
Servo Motor Repair Services Offered by Lincoln Service
At Lincoln Service, we are dedicated to delivering comprehensive servo motor repair services that cover a broad range of needs. Our services include:
- Thorough Diagnostic Testing
Before any repair work begins, our team of technicians conducts detailed diagnostic testing to identify the root cause of the motor malfunction. Utilizing top-of-the-line testing equipment and techniques, we can accurately diagnose issues affecting the performance of the servo motor. This ensures that our repair work is precise and efficient.
- Skilled Repairs and Component Replacement
Once the diagnostic testing is complete, our highly skilled technicians employ their expertise to repair the servo motor effectively. Using advanced tools and techniques, we address the identified issues with precision and diligence. We also have an extensive inventory of genuine OEM components, allowing us to replace faulty parts and restore the motor to optimal working condition.
- Preventive Maintenance
At Lincoln Service, we prioritize the long-term performance and reliability of servo motors. We offer preventive maintenance programs tailored to the unique needs of each client. These programs include regular inspections, cleaning, lubrication, and adjustments to ensure that the servo motor continues to operate at its best. By detecting potential issues early on, we help our clients avoid costly breakdowns and extend the lifespan of their servo motors.
- In-house Testing and Calibration
After completing the repair process, we conduct rigorous in-house testing and calibration to ensure that the servo motor is functioning within manufacturer specifications. Our dedicated testing facilities are equipped with advanced equipment and systems that allow us to simulate real-world operating conditions. This thorough testing process guarantees that the repaired servo motor is ready for installation and optimal performance.
- Rapid Turnaround Time
At Lincoln Service, we understand that downtime can be a significant concern for businesses. Therefore, we have implemented streamlined processes and efficient repair protocols to minimize turnaround time. Our team is committed to delivering swift and reliable repairs, allowing our clients to quickly resume operations and minimize disruptions.
- Comprehensive Warranty
We stand behind the quality of our repairs and have great confidence in the capabilities of our technicians. Therefore, we offer a comprehensive warranty on our repair work, providing our clients with peace of mind regarding the longevity and reliability of their repaired servo motors.
- 24/7 Emergency Services
We understand that unexpected motor failures can occur at any time, potentially leading to significant losses for businesses. To address such emergencies, Lincoln Service provides 24/7 emergency repair services. Our dedicated team is ready to respond swiftly to any urgent repair needs, ensuring minimal disruptions and reducing potential losses due to extended downtime.
Why Choose Lincoln Service for Servo Motor Repairs?
Partnering with Lincoln Service for your servo motor repair needs provides various advantages for your business, including:
- Industry Expertise and Experience
With years of expertise in the servo motor repair industry, Lincoln Service has earned a solid reputation for delivering top-notch services. Our skilled technicians possess in-depth knowledge of servo motor technology and the intricacies of different motor brands and models.
- State-of-the-Art Facilities and Equipment
We continually invest in the latest testing equipment, tools, and technologies to ensure that our repair processes are efficient, accurate, and reliable. Our advanced testing facilities allow us to recreate various operating conditions and thoroughly evaluate the repaired servo motors before they are returned to our clients.
- Extensive OEM Component Inventory
To ensure the highest quality repairs, we only use genuine OEM components sourced directly from reputable manufacturers. Our extensive inventory of components allows us to promptly replace damaged parts, minimizing repair time and facilitating quick return to operation.
- Tailored and Customized Solutions
We understand that each client’s needs are unique, and we aim to provide customized solutions that best meet their requirements. Whether your business operates in manufacturing, robotics, or any other industry, our team of experts will work closely with you to develop solutions that address your specific needs, minimizing downtime and maximizing the performance of your servo motors.
- Commitment to Customer Satisfaction
Client satisfaction is at the forefront of our operations at Lincoln Service. We strive to build long-term relationships with our clients based on trust, transparency, and exceptional service. Our team is dedicated to providing prompt and reliable customer support, offering a seamless experience throughout the repair process.
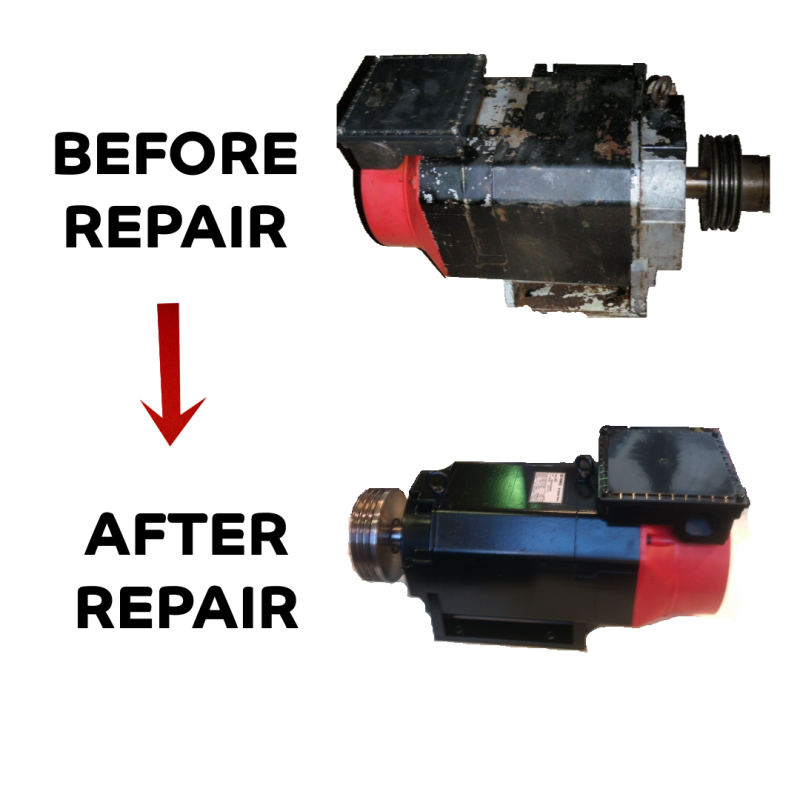
At Lincoln Service, we recognize the critical role that servo motors play in modern industries
Our comprehensive servo motor repair services are designed to optimize the performance and reliability of these essential components. By leveraging our expertise, state-of-the-art facilities, and commitment to excellence, we ensure that your business experiences minimal downtime, reduced costs, and improved productivity.
When it comes to servo motor repairs and preventive maintenance, Lincoln Service is the ideal partner to trust. Contact us today to learn more about our services and how we can help your business achieve optimal performance and longevity for its servo motors.